Production / contract manufacturing
All about pipes and sheet metal
.jpg)
Component production and laser work, also on a contract basis
Laser welding systems for small to medium-sized components
Little to no distortion due to laser welding
Ideal for thin-walled stainless steel sheets and pipes
Batch size "1" up to thousands of pieces
Mechanical or chemical weld seam cleaning
Packaging and labeling according to customer specifications
.jpg)
Laser welding
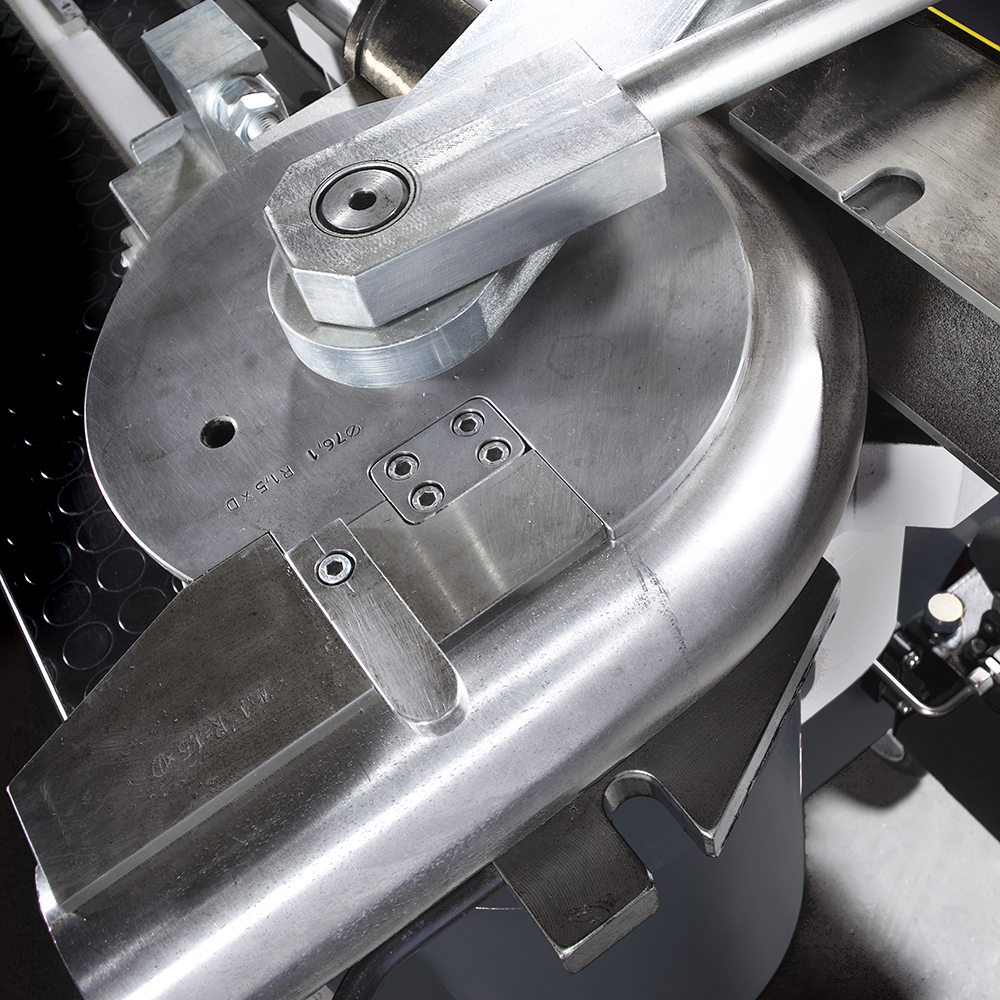
SOFTWARE AND CAD PROGRAMMING INCLUDED
CNC tube bending of thin-walled stainless steel tubes up to 3.0 mm
Diameter 38.0mm - 168.3mm
Radius 100mm - 1,500mm
Material: 1.4301 (1.4404 and 1.4571 on request)
Over 100 different bending tools available
Leg extensions and ends Machining according to customer specifications
Custom-made products from one piece
Drawing creation and programming included
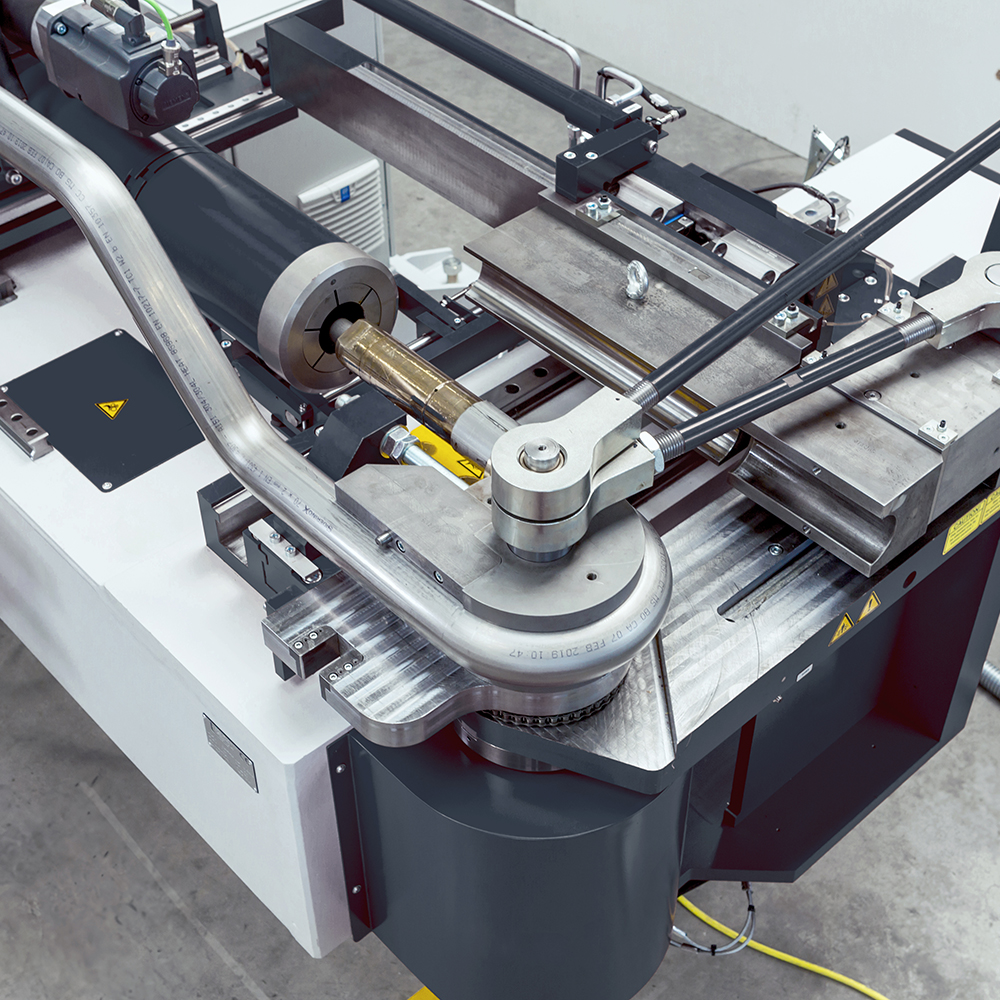
Tube bending
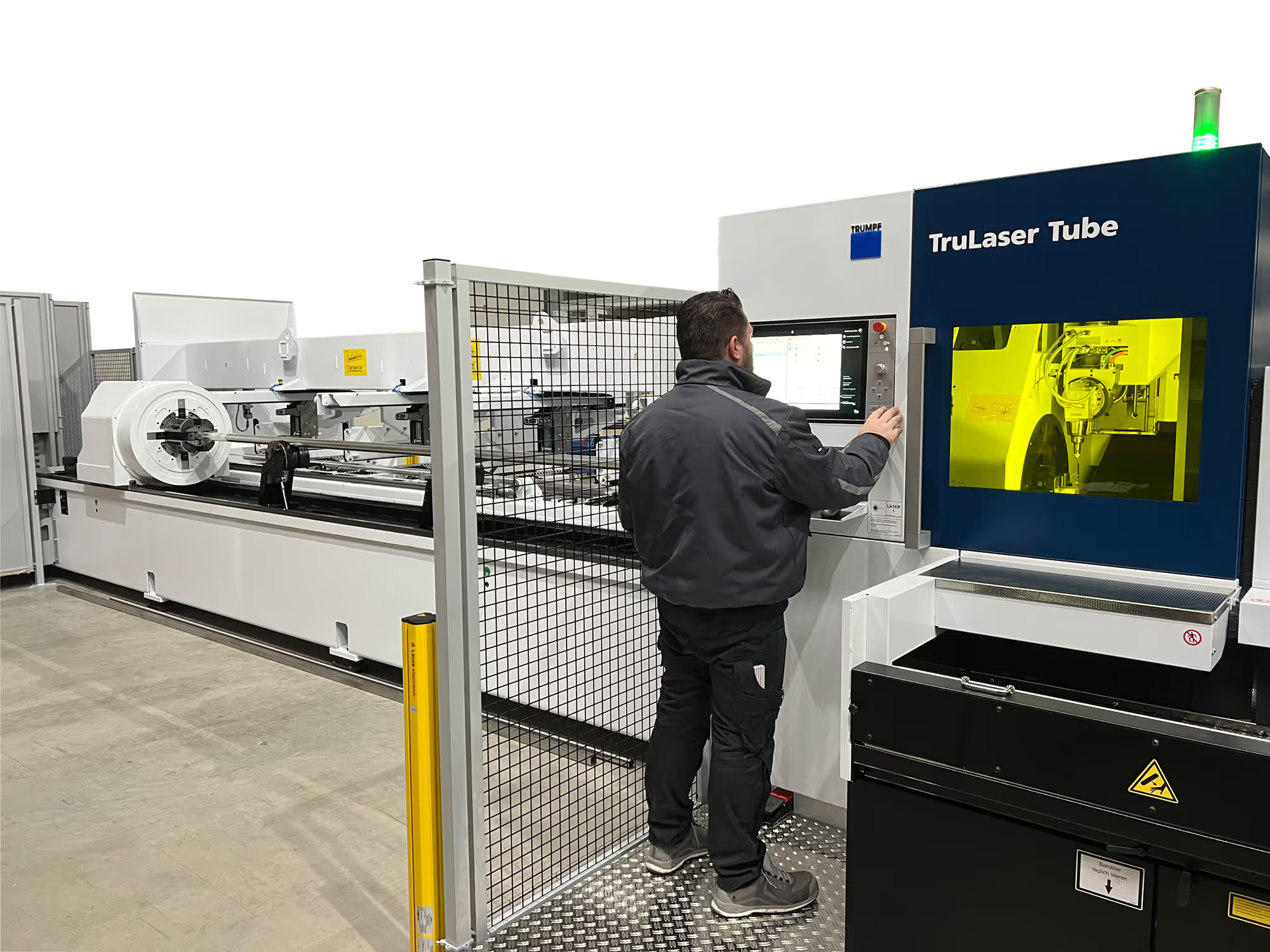
© Trump
REGIONAL. ACCESSIBLE. FAST.
Trumpf TruLaser Tube incl. bevel cut up to 45° - ideal for welded assemblies
Laser cutting of aluminum and stainless steel with 4mm wall thickness
Maximum pipe diameter 168.3 mm / square pipes up to 150 mm side length
6 meter loading and 3 meter possible finished part length
Intelligent material division and the latest laser quality for penetration, burr and speed
Contract laser work as required incl. cleaning and deburring
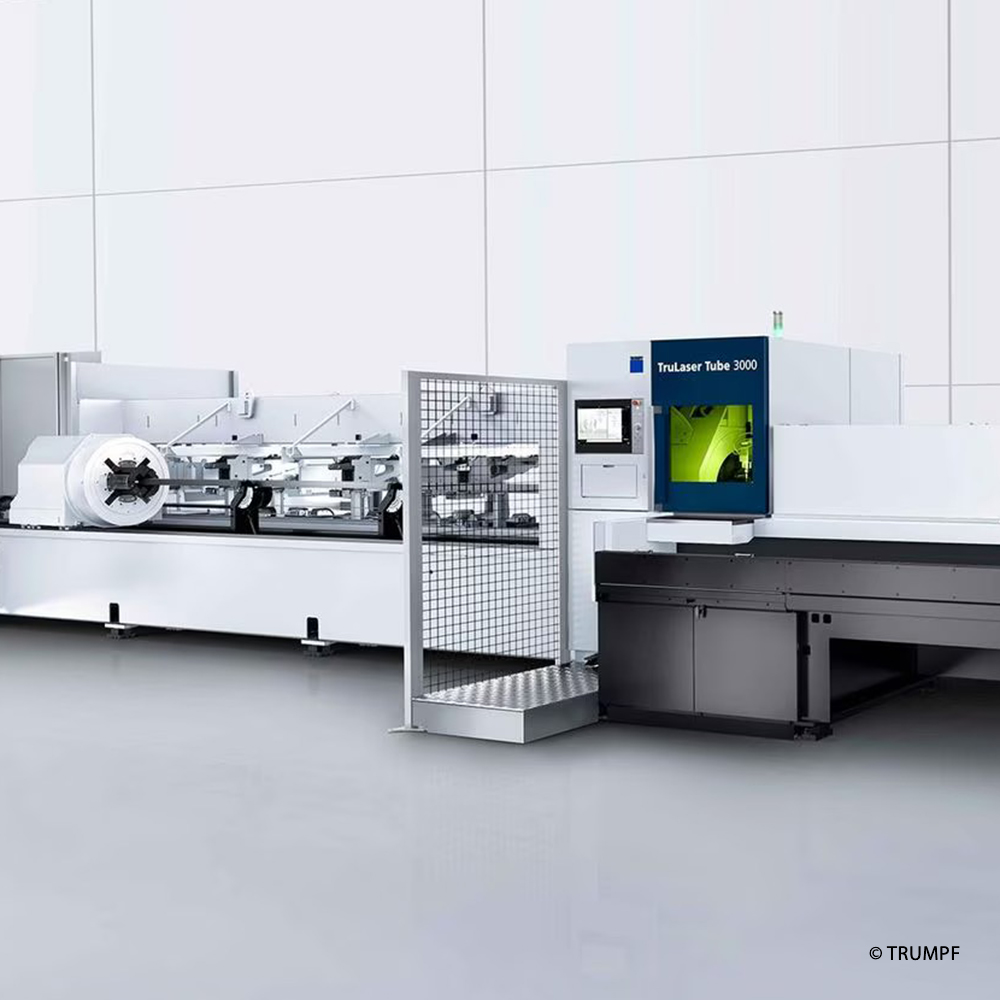
Laser tube cutting
.jpg)
STAINLESS STEEL AND ALUMINUM SHEETS UP TO 15MM
Trumpf TruLaser with BrightLine fiber cutting technology for the best cutting results
Maximum sheet size 3000x1500x15mm (stainless steel and aluminum)
Series production up to batch size "1" Production at economical conditions
Best cutting results thanks to PierceLine and Nanojoints, even in
HighSpeed cuttingDeburring and cleaning according to customer specifications
.jpg)
2D LASER CUTTING
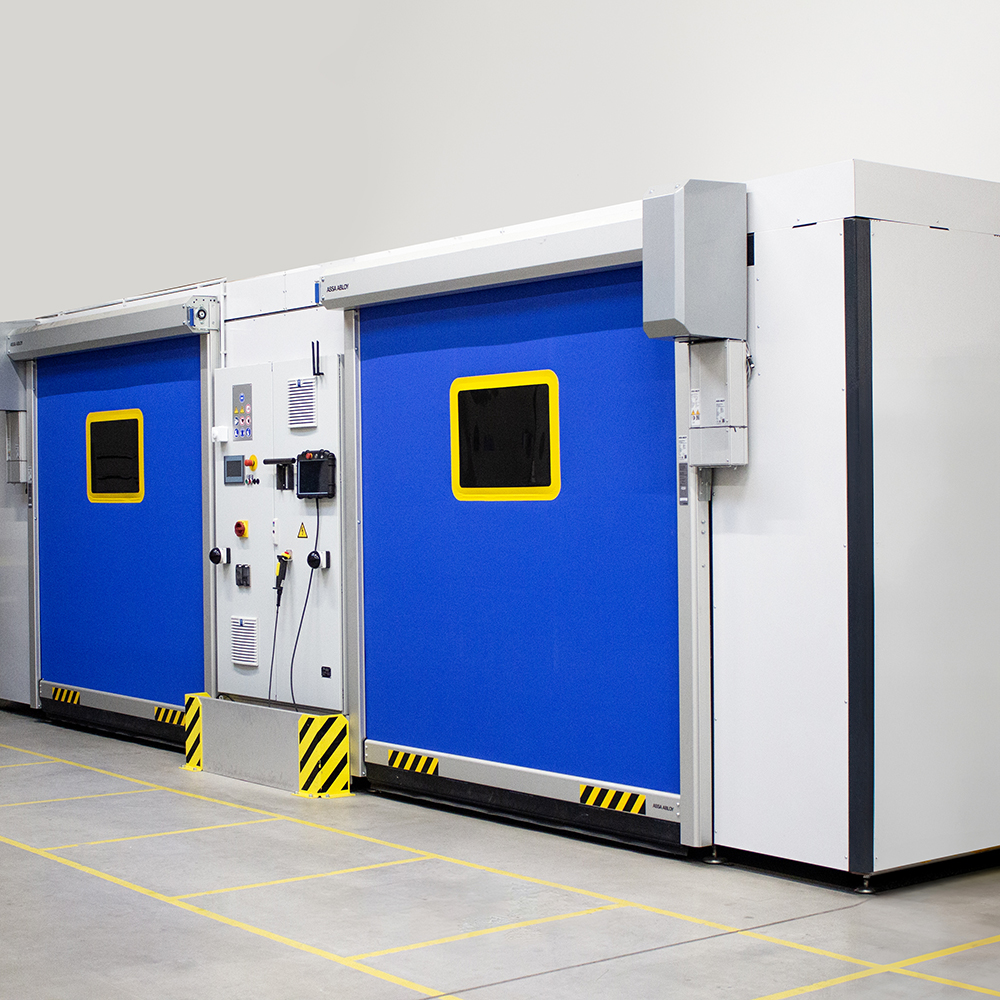
Stainless steel and aluminum pipes up to a diameter of 168.3 mm
Parallel robot welding with state-of-the-art welding source
Automated aluminum and stainless steel welding
Incl. fixture construction for small and medium batch sizes
Special welds by hand welding
.jpg)
ROBOT WELDING
.jpg)
PICK-UP AND DELIVERY SERVICE
Turning and milling work for customized special parts
In combination with tubular and flat laser components
Welded assemblies in individual and series production
Automatic lathe up to diameter 65mm as bar stock
Milling machine for small and large series
.jpg)
Turning and milling
Your direct contact
.jpg)
Martin Cichon
Head of Production
+49 9341 848 550-6
martin.cichon@michel-tube.com
Save vCard