Know-how
What you should know about pipes and hoses...
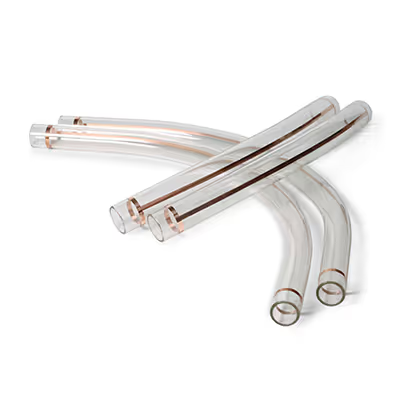
When do I use a glass pipe bend?
The answer
A glass pipe bend is used when conveying abrasive, usually glass fiber-reinforced materials - for example polyamide. A glass pipe bend must be used, especially where space is limited and radii are small. If this is installed stress-free and is not mechanically damaged, it can be expected to last for years. This is particularly advantageous when installation space is limited and accessibility is poor.
To prevent static charging, a copper tape is glued to the outer radius to transfer the charge via the pipe and earthed at the end of the pipe.
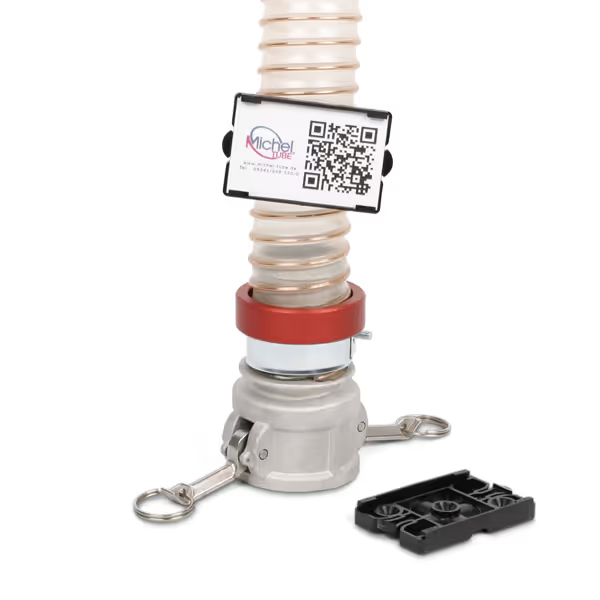
Why is proper earthing so important?
The answer
Bet that ???
At least one hose in a plastics processing plant is not earthed? We would like to make this bet - "for a roll of hose"...but first to the origin.
Why is that? Quite clearly. It has to be done quickly. And if something has to be done quickly, the hose is quickly "put over it" - the main thing is to get the machine running again after a standstill. Then the right equipment is often not at hand. The spring steel wire is difficult to expose - the risk of injury when exposing and bending is very high.
Incidentally, staff are not aware of the importance of earthing or have not been trained in this area. For additional safety and visual control, we therefore recommend a worm drive clamp with integrated earthing. The cable can be laid statically. The clamp is fastened and tightened over the hose after the hose has been replaced (and hopefully after the wire has been folded over, which is officially not 100% correct). The screw also drills into the spring steel wire and provides additional earthing and a visual check at the same time! - Better safe than sorry and, above all, protects the end devices including controls etc..
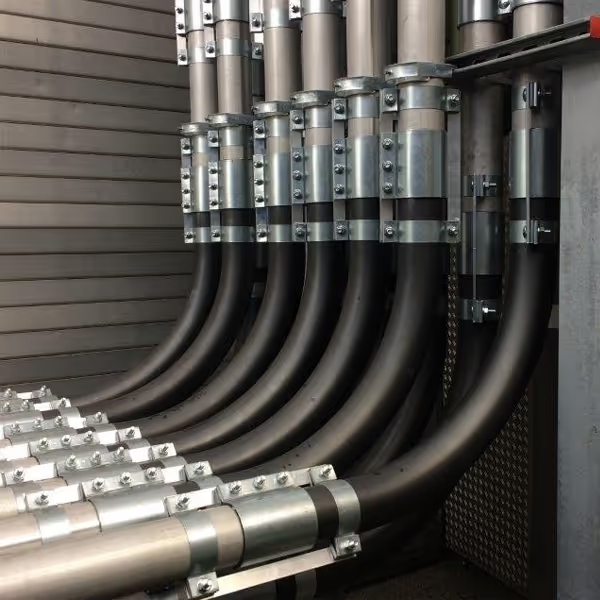
How can wear and tear be easily minimized?
The answer
Unfortunately, smaller radii and leg extensions are always used and installed in practice. This is mainly due to space and cost reasons. However, it is important to know that the radius contributes significantly to the durability of the bend and to the gentle conveying of the granulate and ultimately to the safety of the conveying and production process. The larger the radius, the more "homogeneous" the material runs around the curve. The smaller the radius, the more unevenly and with more contact points the pellets bounce around the curve.
Wear occurs particularly in the run-out zone. And this is exactly where a sufficient leg extension is very important, as the wear in the run-out zone is very heavy. So if it is possible to install a large radius with long legs for space reasons, we definitely recommend it! Think long-term and about the accessibility of the system's pipes. Installation time and repairs are time-consuming and expensive!
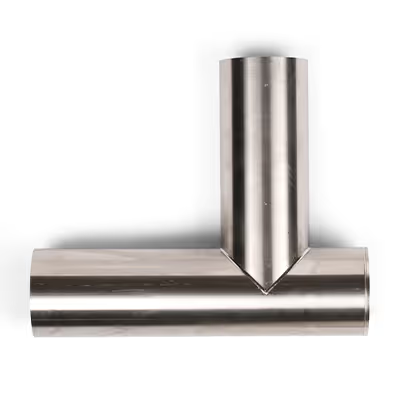
How do I install a closed T-piece correctly?
The answer
A closed T-piece serves as a speed brake and thus reduces wear in the devices or on the separator, as the material hits at a lower speed. In addition, a closed T-piece can also be used where there is very little installation space or can be partially installed in front of a hose to reduce wear in the radius of the hose.
A closed T-piece is always installed so that the material hits the closed part of the pipe - the cover - in its conveying direction.
As there is a gap between the cover and the pipe outlet, there is an area that fills with material. The inflowing granulate is thus guided around the bend on the material (material on material). This reduces wear and reduces the formation of angel hair.
The material is sucked out of the closed area when the pipe is completely empty or at the end of conveying. No residue remains in the pipe.
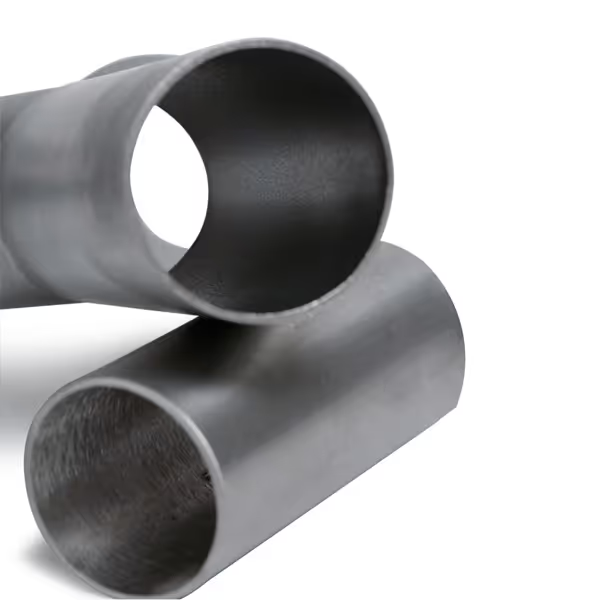
When does angel hair formation occur?
The answer
Angel hair formation occurs as soon as granulate is conveyed over long distances at high speed. The granules hit the inner wall of the pipe at a shallow angle and, depending on the granules, the heating/friction causes them to pull threads, known as angel hair. As soon as angel hair occurs in large quantities, it can lead to blockages during conveying, which jeopardizes the process and cycle times.
One possible remedy is an internally blasted conveyor pipe in which the so-called "fish skin effect" has been created. A small "protective film of air" forms on the inside of the pipe due to turbulence, which means that significantly less granulate comes into contact with the inner wall of the pipe. Another alternative is the use of hoses, but this significantly reduces the conveying capacity.
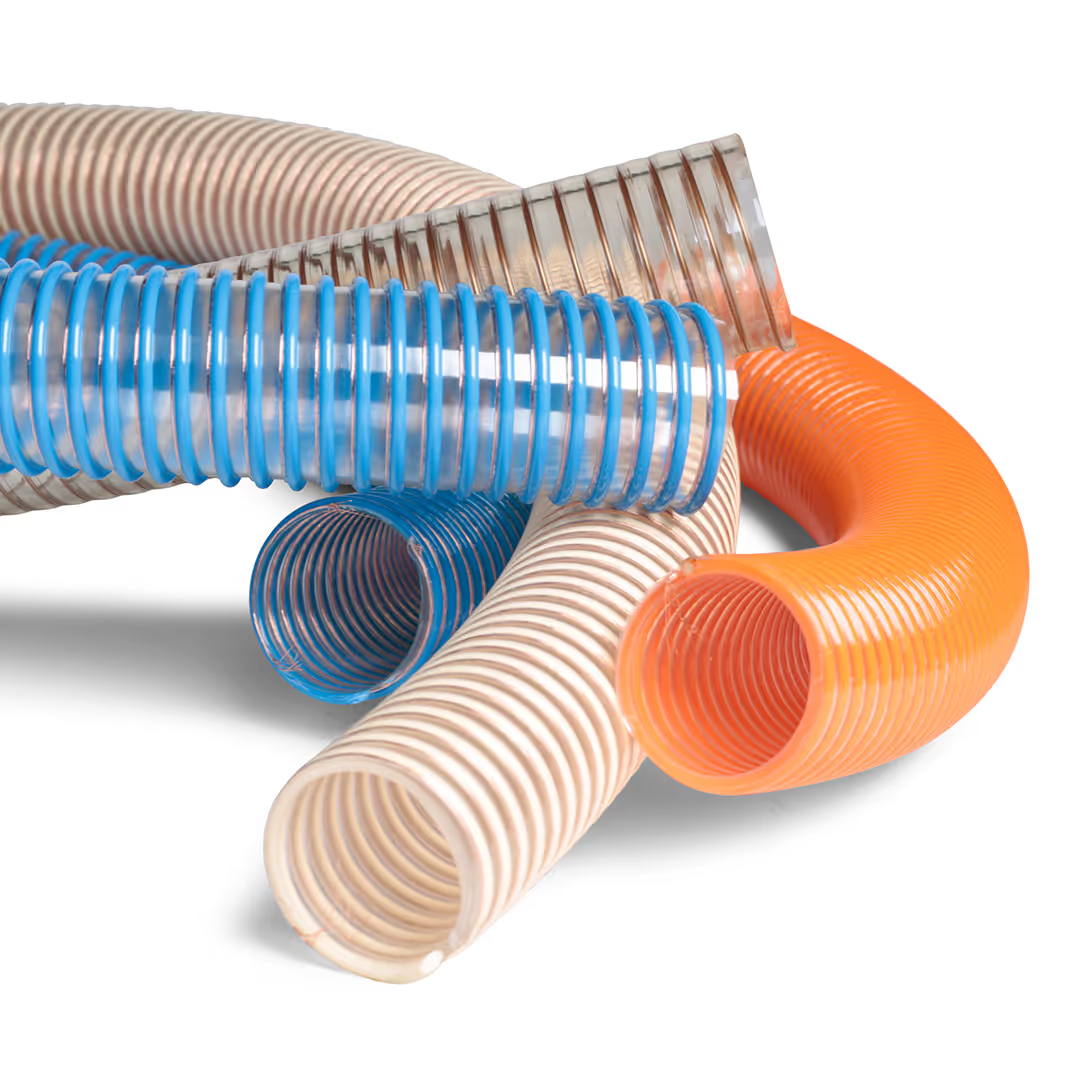
Which hose is the right one?
The answer
First of all, the material conveyed determines the hose type / wall thickness that should be selected. Then the flexibility and accessibility factor comes into play. A thick wall thickness makes hoses less flexible, but a thicker wall thickness protects against rapid wear.
In addition to the hose type, the service life of a hose can also be significantly extended with the correct hose length and installation situation. If the material is slowed down before the hose (by a pipe bend or a closed T-piece that guides the material around the bend), there is less friction in the hose - a hose should also never sag completely, because a "sharp bend"/ a tight curve is often created at the pipe socket, which is unnecessarily stressed by the granulate.
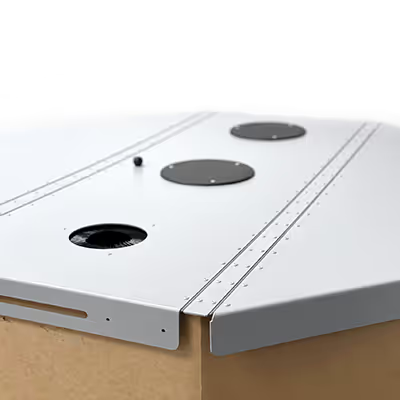
Why should an octabin cover be used?
The answer
In practice, a lot of granulate is packed in octabins and delivered to plastics processing companies. The large container has many advantages over bagged goods - but also a major disadvantage - handling.
By handling, we do not mean the transportation of the octabin, but the handling during the suction process. The octabin is often opened and a suction lance inserted. As the amount of material decreases, the suction lance "eats" its way down bit by bit. Depending on the height of the octabin, the length of the suction lance and the flow behavior of the granulate, this happens sometimes better and sometimes less well.
Another major disadvantage is the material contamination that can occur when using octabins. If octabins are often placed under platforms or pipelines, foreign materials and impurities, including metal objects, can quickly fall into the octabin. This happens in particular if, for example, a cutter knife is used to cut a window/cut-out in the lid of the octabin for a suction lance.
A remedy for all these problems, which can also be really expensive, is the seal-IT foldable octabin cover. The cover is maintenance-free, lightweight, foldable and can therefore be installed in just a few seconds.
The folded edges of the cover ensure mechanical stability and prevent it from slipping, especially at tipping stations.
The modular, configurable suction openings guide and improve the suction process, minimizing downtimes and malfunctions.
The cover prevents contamination from foreign bodies, which - for whatever reason - often end up in the granulate in practice. Likewise, seal-IT promotes the conscious handling of granulate and protects hygroscopic materials from absorbing moisture - which saves time, energy and therefore money during drying.
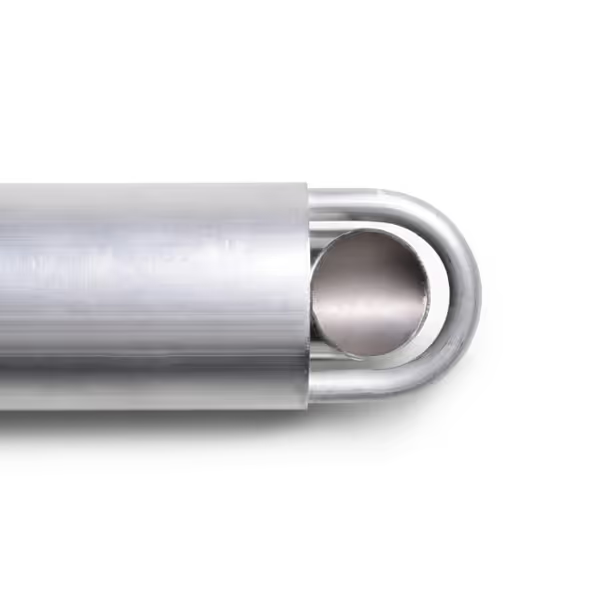
Why is the correct setting of a suction lance so important?
The answer
A suction lance is one of the "cheapest" components of a material conveyor system. However, if set incorrectly, it can lead to major problems and malfunctions in the system.
For example, if the lance is not clean and correctly adjusted to the material, too much or too little material is conveyed, which leads to a malfunction in the injection molding machines.
If the length of a suction lance is too short, clean suction is not possible because the lance tilts. This also makes it more difficult to empty the container.
If the suction lance is selected in the wrong material, it will be subject to wear and the conveying process will be disrupted by failures.
At Michel Tube, we have numerous suction lances in a wide variety of lengths and materials in our portfolio.
Do not hesitate with your inquiry and ask explicitly for special lengths or special designs.
.avif)
Why does a glass pipe bend last longer than a wear-resistant pipe bend?
The answer
A glass tube bend from Michel Tube has a wall thickness of 5mm. This is hard throughout. Stainless steel with a wall thickness of 1.5 mm or 2.0 mm is the starting material for a wear-resistant elbow.
In this comparison alone, the glass elbow already has three times the wall thickness.
Despite a complex treatment, the stainless steel pipe bend only achieves an increased surface hardness. If this is never damaged, the elbow will last almost "forever" - but if it is worn away by the material, a weak point is created that continues to wear.
If a glass pipe elbow can be used due to the requirements and dimensions, this is highly recommended.
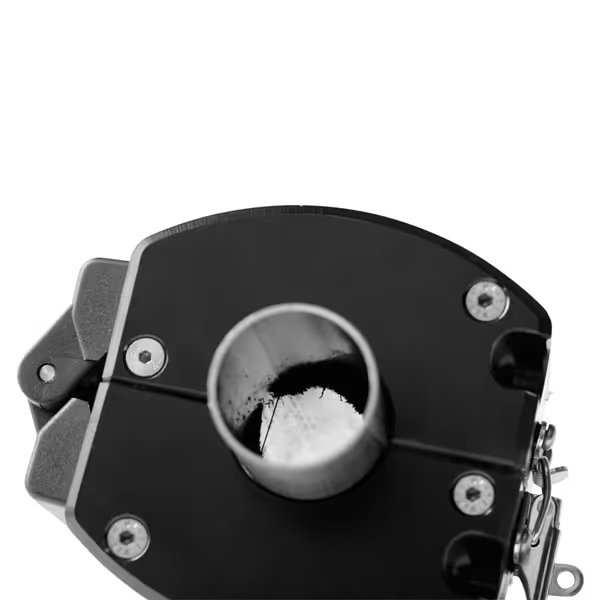
Is there a retrofittable magnetic separator?
The answer
The MAG 14.000 hinged magnet offers a simple way to filter ferritic impurities from the granulate. The magnetic separator can be subsequently folded around a pipe and - thanks to the principle of a magnetic tunnel - captures all ferritic impurities on the inside of the pipe.
This means that the material is not contaminated, the flow is not restricted and there is no need for complex installation work.
The only requirement is a suitable discharge point after the magnet (e.g. a hose coupling point where the impurities can be discharged). By releasing the magnet - during the conveying pause - the magnetism on the pipe is removed and the components fall out at a suitable point (hose coupling point).
The MAG 14.000 is scalable, mobile and functions independently. A perfect, simple, understandable and important addition to any material conveying system.
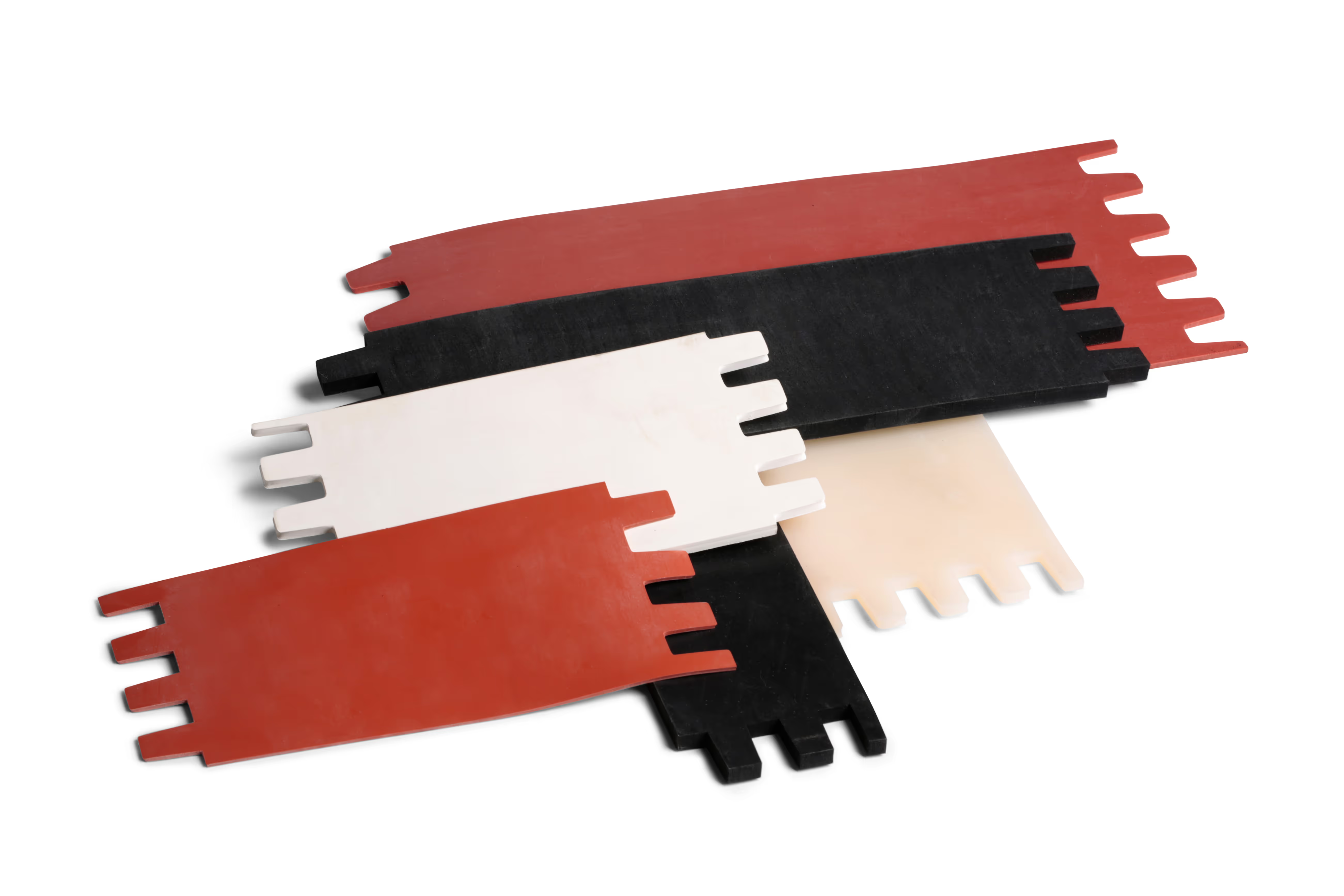
When do I use which seal?
The answer
There are many different gasket qualities. The right choice of gasket depends mainly on the temperature and the requirements for the gasket (FDA conformity). The standard gasket for a pipe coupling is SBR black. The temperature range is max. 80°C (short-term). Although 60°C should not be exceeded in the long term. If higher temperatures are required, EPDM max. 120°C (for a short time) can be selected. However, it is usual to use a silicone seal (short-term) 230°C.
This is frequently used in pipework in dryer construction. If there are requirements for FDA conformity, we recommend our light-colored EPDM gaskets. In general, there are many gaskets available in a wide range of qualities. Our experts will be happy to help you choose the right gasket. The function of a gasket is often underestimated - so if in doubt, please contact us.
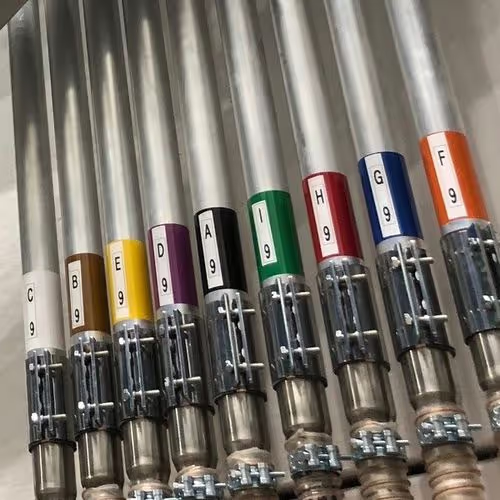
When do I use a pipe connector and when do I use a pipe coupling?
The answer
Our so-called pipe connectors are mainly used for suction / vacuum conveying. A standard pipe connector is 100 mm long and is tightened with two M8 screws. The purpose of the pipe connector is to connect the pipes tightly. The small, inexpensive design is also ideal for confined spaces and large projects where costs play a major role.
pipe couplings can also be used for pressure conveying and - depending on the diameter - can be subjected to pressures of up to 6 bar. However, it is important to know that pipe couplings only seal the pipe and cannot absorb any axial force - i.e. a force or pressure surges in the direction of the pipe, for example. In the event of axial forces or vibrations, a strain relief must also be installed.
Pipe couplings can be produced in lengths of up to 300 mm. Another characteristic feature is the double, toothed inner jacket made of sheet metal, which has a positive effect on assembly/disassembly and on the seal. Seals are generally available in black standard quality or in light FDA quality. Special seals for specific requirements are also available at short notice.
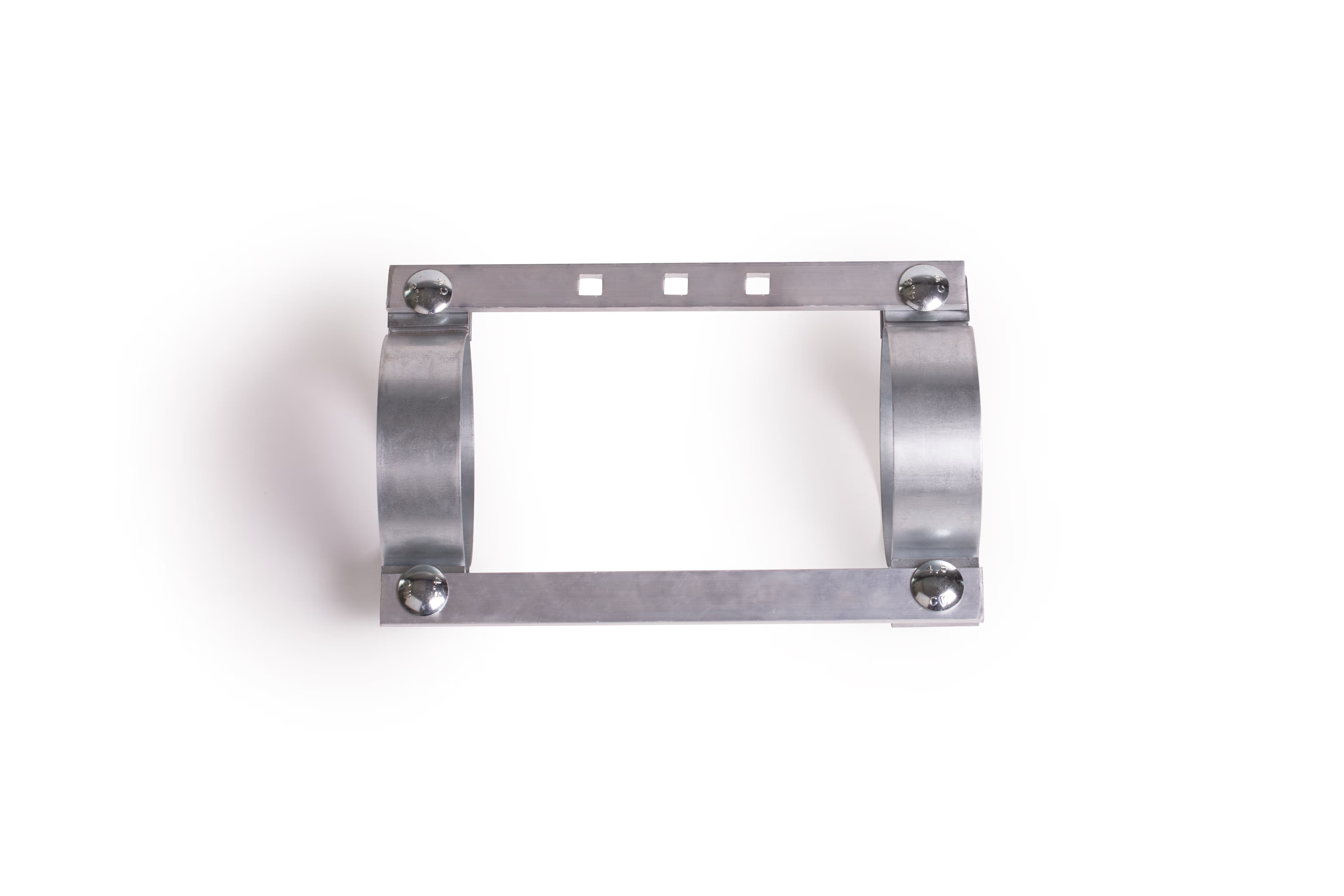
When is strain relief required?
The answer
Strain relief is particularly important as soon as pressure and/or pressure surges occur. A pipe coupling only has a sealing function. The flat gasket seals the pipe gap. The pipes cannot be held against axial slippage, which is why strain relief is strongly recommended in the event of pressure.
Pipe couplings can also be used for pressurized delivery and - depending on the diameter - can be subjected to up to 6 bar. However, it is important to know that pipe couplings only seal the pipe and cannot absorb any axial force - i.e. a force or pressure surges in the pipe direction, for example. In the event of axial forces or vibrations, a strain relief must also be installed.
A strain relief can be retrofitted around the pipes. It visually encloses the coupling, so to speak, and prevents the two pipe ends from slipping. Please do not underestimate the forces that occur during pressure conveying and fasten the pipes adequately and properly. Our experts will be happy to answer any questions you may have.
.avif)
How can I clean a pipe?
The answer
Cleaning balls are used to clean the inside of pipes in the plastics industry. This is particularly important as there must be no incorrect material in the pipe to avoid quality losses or a faulty production process due to material contamination and to comply with certifications.
Before changing the material, the cleaning balls are inserted into the pipe during the set-up phase, run through the entire pipe and are ejected again at the end. This process should be repeated several times.
The cleaning balls are available in various diameters and qualities - FDA-certified cleaning balls are also available.
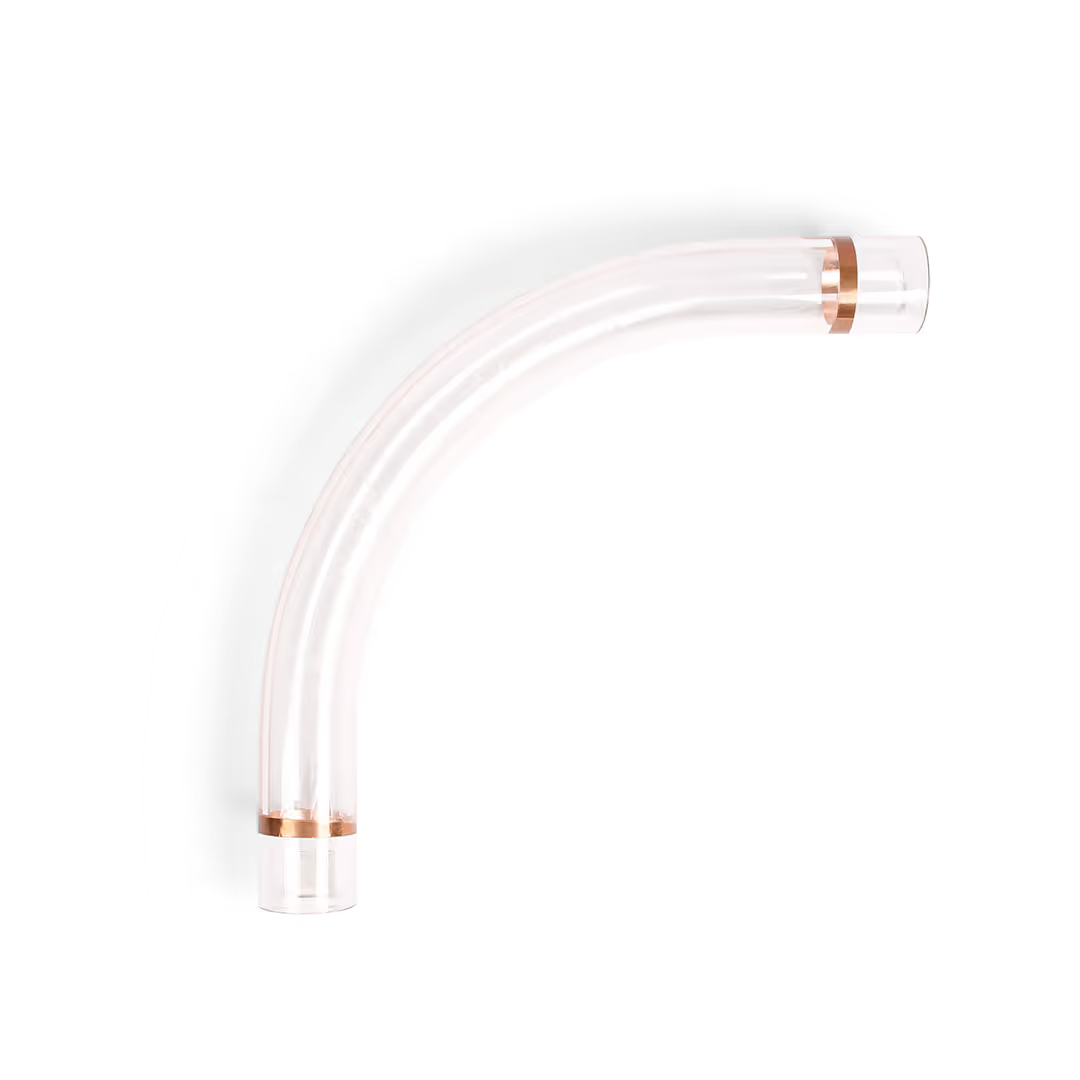
Can I see through a glass pipe bend?
The answer
The myth that the material can be observed through a glass pipe bend has unfortunately been around for a very long time. The fact is that after a few days and weeks, the inside of the glass arch becomes so clogged that no more material can be seen in detail. Only a flow of material can be seen.
To compare the glass pipe bend with a sight glass / window pane is unfortunately wrong.
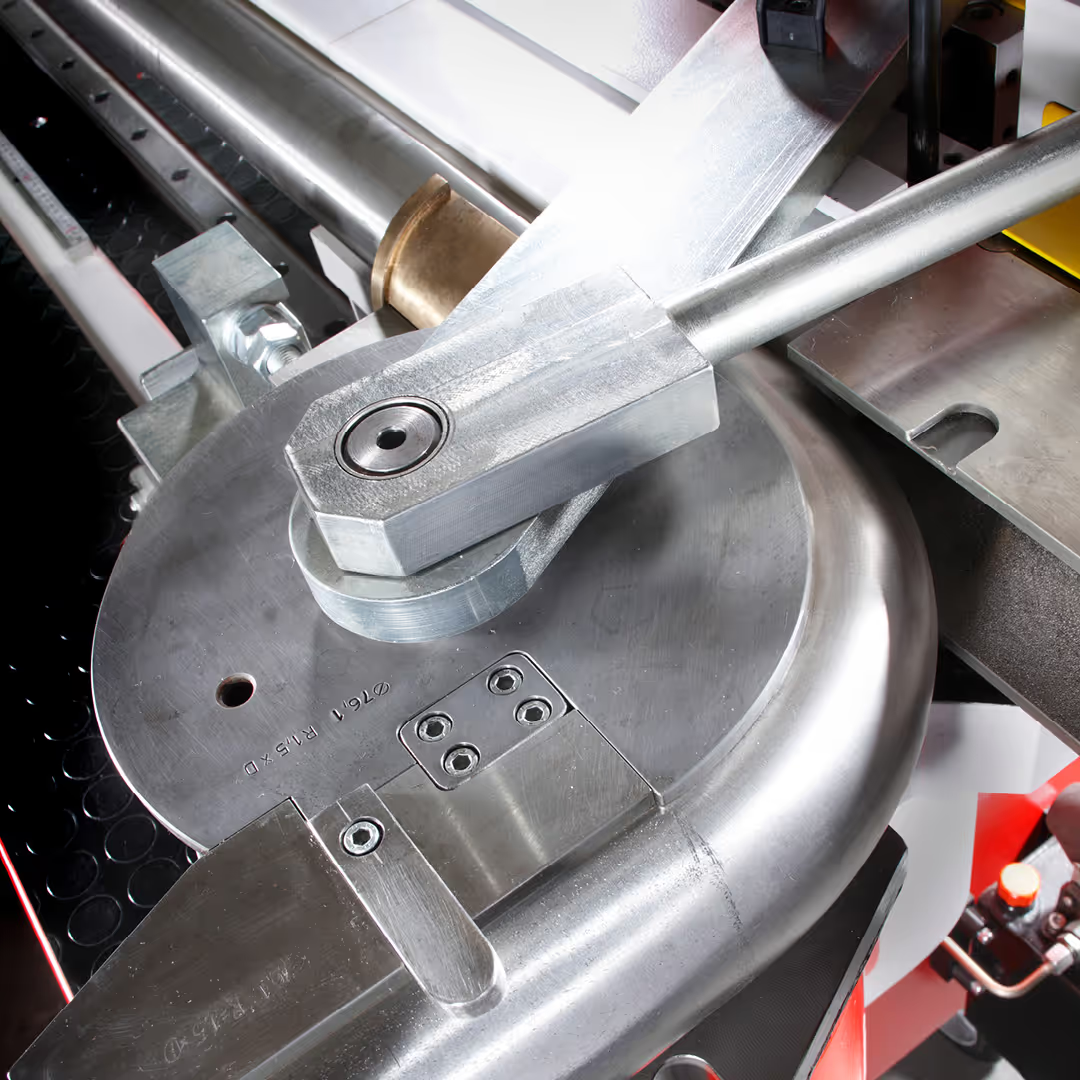
How is a stainless steel pipe bend bent?
The answer
We bend a stainless steel pipe bend using a so-called mandrel bending machine. The stainless steel tube is placed over a bending mandrel, which prevents the tube from collapsing during bending. The mandrel consists of articulated parts, is slightly smaller than the tube inside and can be lubricated.
After the lateral supports (slide rails) have been moved to the tube and it has been clamped at the front with the clamping jaws, the bending process begins with a rotary movement around a bending tool / negative that reproduces the radius.
Meanwhile, the so-called crease smoother ensures that no waves form on the inside of the tube (on the smaller radius) in the case of small radii. This can happen quickly, as pipes with thin walls are bent.
To facilitate the bending process, it is advisable to lubricate sufficiently. Ideally, the seam of the pipe should be in the so-called "neutral position" so that the pipe seam is neither stretched nor compressed.
After the bending process, the bending machine returns to the home position. The bend bounces slightly and can be removed to be calibrated and washed.